
blog
Does The Flame Cutting have Already been Eliminated?
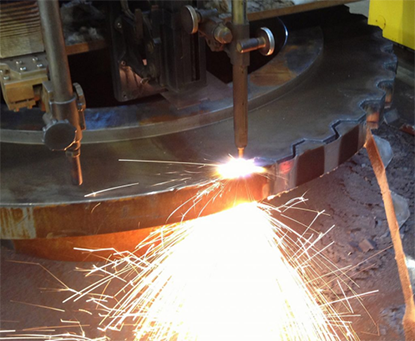
Share:
Facebook
Twitter
Pinterest
LinkedIn
Contact Us

Contact: Mr Liu
Whatsapp/Mob/Wechat:008613394110095
Email:liu@weldcnc.com
Most Popular
Get The Latest Updates
Subscribe To Our Weekly Newsletter
No spam, notifications only about new products, updates.
Product Catalog
Request a Quote
Ready to Work Together? Build a project with us!
Learn More From
Frequently Asked Questions
Please tell us what you want to mark, the size and desired power and other information.
Yes, we will, English manual and video will come along with the machine.You also can contact our service team if you need any help during use our machines.
Delivery time is 20-30 days after receiving the deposit
You can make the payment to our bank account, Western Union or PayPal:30% deposit in advance, 70% balance against the copy of B/L.
Read More